Company Insight
Lithium batteries all around the world, monitored in real time from Italy
Klaus Dengler, Managing Director Europoles Suisse GmbH), René Vuillemin, (Managing Director Europoles Suisse GmbH)
The remote monitoring service offered by Flash Battery, European leader in the production of lithium batteries for industrial machines and electric vehicles, is revolutionising lithium batteries.
The applications and market for lithium batteries are fast expanding, and the growth rate is expected to continue to increase.
Ever more manufacturers of industrial machines and electric vehicles are choosing lithium batteries, driven by the improved performance offered by this metal. Tesla, first and foremost, has created a clear gap between itself and other vehicle manufacturers by creating the first true electric saloon in history. Its motors are powered by lithium battery packs which offer a range of over 500 km with an acceleration from 0 to 100 km/h in just 2.7 seconds.
Lithium is the lightest metal on the periodic table, as well as the least dense solid element with the highest electrochemical potential, making it a fundamental material in battery manufacturing. These characteristics make it a perfect, powerful component for the batteries of the present as well as the future.
Improved performance and duration are the goals which drove Marco Righi and Alan Pastorelli, then in their early twenties, to perform their first tests on lithium batteries back in 2009. These initial experiments eventually led to the creation of Flash Battery in 2012, and the company is now the leading European manufacturer of lithium batteries for industrial machines and vehicles.
Everything started with electronics
But the company’s origins were cemented even further back, when the young men’s main passion was electronics.
In 1985, Marco Righi’s father founded what would become the leading European manufacturer of high-frequency battery chargers. The idea that the family company would be handed down to the only son appeared to be Marco’s destiny, and so he started working on the foundations for his future career in the field of electronics. But in 2006 this all changed.
The company was sold, and his dream of carrying on his father’s work was shattered, along with the possibility of continuing in the field. His professional career took another path, but never entirely diverged from the field of electronics.
The first great challenge which seemed impossible
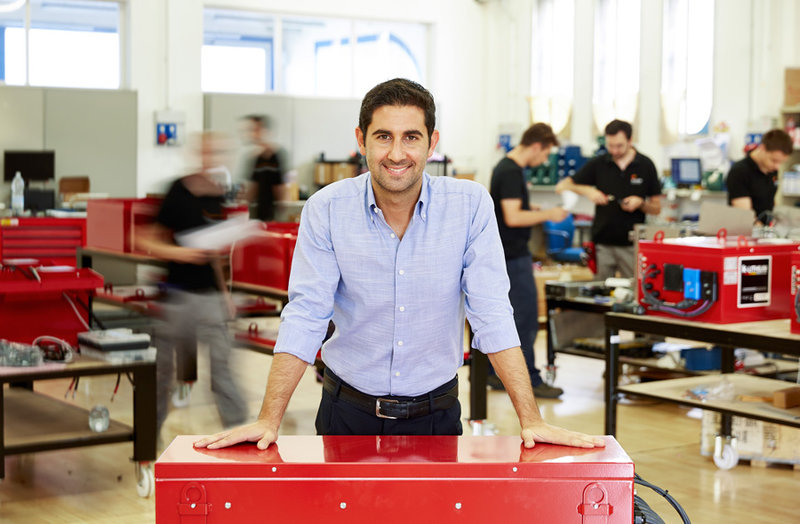
caption
The first significant encounter with lithium batteries occurred when Marco Righi, now CEO of Flash Battery, visited a friend’s company which was building a prototype electric vehicle. On paper these new lithium cells were astonishing – they weighed three times less than the lead-acid batteries used up to that point, while lasting three times longer!
However, the batteries did not provide the expected results. They did not look great, the cells were inconsistent and the internal electronics were inadequate. This experience led to the light-bulb moment: analyse and eliminate the technical issues to create a different control and management system for lithium batteries.
“At that point, I brought in my friend from our days of garage experiments, Alan Pastorelli (who in the meantime had graduated with a degree in electronic engineering and was working in the automotive industry), and we wasted no time. We began working on the design of our lithium battery management system every evening and every weekend.” Marco Righi, CEO and Founder of Flash Battery, recalls.
Sèbastien Hoyos – Export Sales Manager of Charlatte Manutention
That was in 2012, and it was then that we officially began distribution of our Flash Battery lithium batteries.
The first record
In November of the same year, the company took its first big step: in partnership with Vantage Power Global, a Chinese company operating in the automotive sector, it broke the world range record in the field of sustainable mobility, 800 km in a single charge for an all-electric vehicle.
The first remote monitoring project
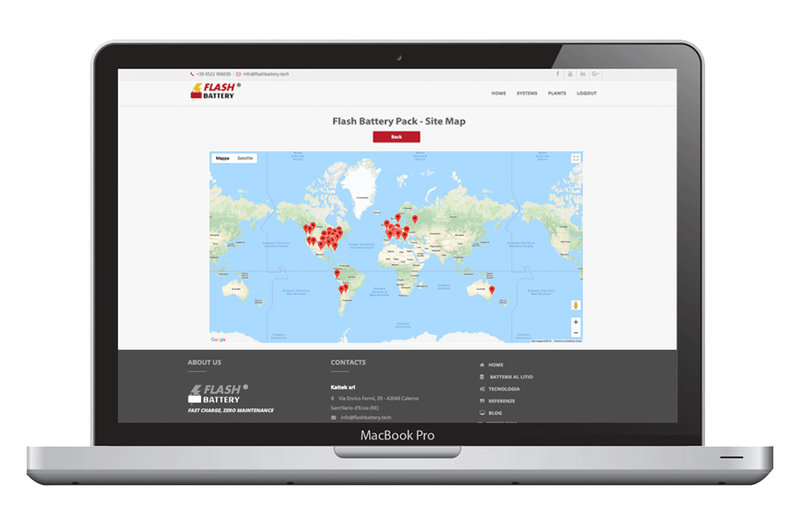
caption
In 2014, Flash Battery began supplying production batteries to what had become one of its main customers in the industrial machinery sector. Elettric80, with a turnover of around 300 million Euros and 11 worldwide subsidiaries, is specialised in the creation of integrated, automated solutions for the tissue, beverage and food sector, such as robotic palletisation systems and automatic laser guided vehicles (LGV). The need to be able to monitor and check the status of the batteries sent to all corners of the world is of fundamental importance for a multinational of this type, and Flash Battery’s remote monitoring allows precisely this.
Remote monitoring of each individual battery, analysing all data received, allows faults to be prevented and makes it possible to organise any extraordinary maintenance operations identified in a timely manner.
When a fault occurs with a traditional battery, the system or machine may suffer days of downtime while a repair is organised. The service department is only notified when the machine stops working, and at that point it is necessary to make travel arrangements for the technician to arrive on site, understand the problem and fix it – assuming, of course, that the components are available! There is no way to know in advance if and when a traditional battery will stop working. With Flash Battery’s remote monitoring, however, we can monitor the operation of the battery in real time and solve 93% of faults before they even happen! An automatic alert system notifies the Flash Battery service centre of any issues, allowing us to intervene in a timely manner and fix the problem before machine stoppages occur.
In 2015, Elettric80 joined Flash Battery’s board, allowing us to perfect two important features: fast charging with consequent increased system efficiency thanks to a decrease in charging times, and Flash Data Center, our software, designed in house, which monitors and analyses the status of our batteries on a day-to-day basis.
Flash Battery’s lithium batteries are used in all Elettric80’s laser guided vehicles – we now perform remote monitoring of 1170 LGVs located in 42 countries around the world.
Watch the video of an Elettric80 system equipped with Flash Battery lithium batteries
This year, Tesla has chosen Flash Battery and its remote battery monitoring for the Tesla Destination Tour. This is the first fully electric tour, which will see the most famous electric supercar in the world, the Tesla, used over 12 stages across Italy. In fact, the power for the trailer coupled to this prestigious Californian car, which powers a mobile kitchen, is provided by a 10.2 kWh Flash Battery lithium battery. More details here.
“Right from the very first experiments in my garage,” notes Marco Righi, CEO of Flash Battery, “We believed that lithium batteries had the potential to replace traditional batteries and thus improve the performance of industrial machines and vehicles. Thanks to our special active and passive electronic balancing system combined with remote monitoring, we have made this technological change much easier than before.”
The size of our remote monitored battery network
Since Flash Battery was founded in 2012, over 4500 lithium batteries have been designed and produced, and custom solutions have been developed for over 200 different models.
We have installed 55 MWh across various industrial machinery and electric vehicle applications, and all Flash Battery products, used in 54 different countries around the world, are automatically monitored on a daily basis by our proprietary system, the Flash Data Center.
93% per cent of faults were dealt with in advance and proactively, allowing unnecessary machine stoppages to be reduced. Forecasts for 2018 expect the company to reach 7500 batteries, installing over 90 MWh in various industrial machinery and electric vehicle applications worldwide.
Detect faults before they happen and monitor your batteries anywhere in the world. That’s why companies are choosing Flash Battery.
Flash Battery offers a remote monitoring system that predicts malfunctions and enables the condition of each individual battery to be determined at any time.
- Daily monitoring of the usage of each individual battery
- Continuous and automatic prevention
- Organise extraordinary maintenance and repair operations in a timely manner
- Eliminate maintenance costs data allows you to make improvements to your machinery
- Increase machinery productivity
- Real-time usage
- Alerts in the event of malfunctions
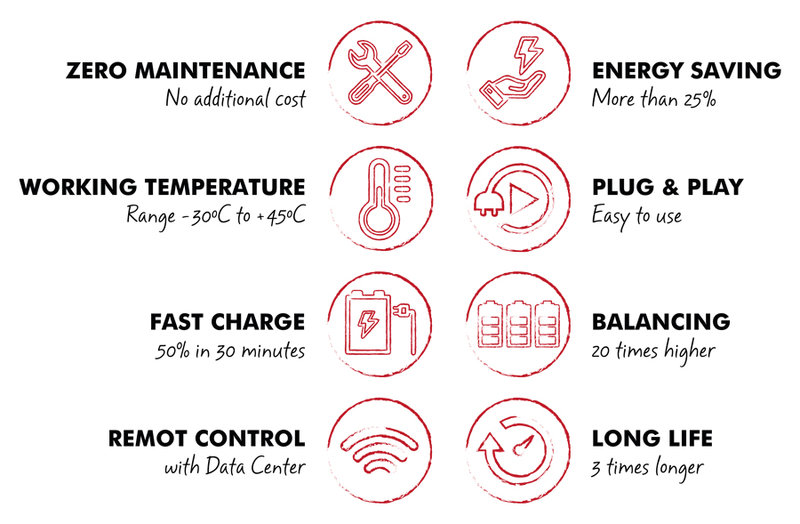
caption
...Beside the attractive commercial offer, Kaitek brought to the table a complete transparency on its technical capacity and knowledge which inspired us to trust this partnership. Kaitek has also shown great flexibility in adapting their product to our machines and applications. Their product is smart and I believe there is a potential growth in this market.
Contact details
Kaitek Flash Battery
Ingolstaedter Straße 51
92318 Neumarkt
Germany
Tel: +49 9181 896-0
Fax: +49 9181 896-1115
Email:info@flashbattery.tech
Website:www.flashbattery.tech
ASK FOR AN INITIAL EVALUATION.
Ask us now for an evaluation of your situation. A Flash Battery specialised technician will get back to you within two business days.